5-3: Night Jumps 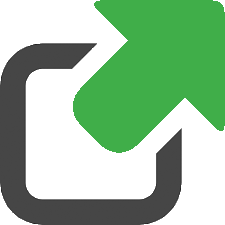
Night jumps can be challenging, educational, and fun, but they require greater care on the part of the jumper, pilot, spotter, and ground crew. As with all types of skydiving, night jumping can be safer with special training, suitable equipment, pre-planning, and good judgment.
Every skydiver, regardless of experience, should participate in night-jump training to learn or review:
- techniques for avoiding disorientation
- use of identification light, lighted instruments, and flashlight
- target lighting
- ground-to-air communications
- emergency procedures
Any jumps made between official sunset and official sunrise are considered night jumps. Jumpers must maintain safety and comply with FAA regulations using this definition. However, night jumps to meet license requirements and to establish world records must take place between one hour after official sunset and one hour before official sunrise.
Skydivers participating in night jumping should meet all the requirements for a USPA B or higher license. Participants should complete a comprehensive briefing and drill immediately before the intended night jump. A USPA S&TA, Examiner, or Instructor who has completed at least two night jumps should conduct this training. This official should sign and document the training, including the date and location, in the jumper’s logbook.
Night jumps can present new and unusual situations, and jumpers must approach this challenge with caution because darkness greatly impairs vision and depth perception, causing the opportunity for disorientation, a different appearance of the earth’s surface, and a lack of familiar reference points. You should be thoroughly familiar with the effects of hypoxia (oxygen deprivation) on night vision found in the FAA Aeronautical Information Manual (AIM) online at faa.gov. One of the first effects of hypoxia, evident as low as 5,000 feet, is loss of night vision. It takes approximately 30 minutes to recover from the effects of hypoxia. Smokers suffer the effects of hypoxia sooner than non-smokers. Carbon monoxide from exhaust fumes, deficiency of vitamin A in the diet, and prolonged exposure to bright sunlight all degrade night vision.
Night vision requires 30 minutes to fully adjust. A jumper’s own shadow cast by the moon can resemble another jumper below and cause confusion. Skydivers infrequently make night jumps and are less familiar with and less proficient in handling themselves under the conditions of this new environment. Since the skydiver cannot perceive what is taking place as rapidly and easily as in daylight, it takes more time to react to each situation.
D. Special Equipment
For protection from aircraft, the FAA requires night jumpers to have a light visible for at least three statute miles displayed from opening until the jumper is on the ground. USPA recommends using constant-beam lights rather than strobes, which can interfere with night vision and depth perception. Constant lights are preferable, but jumpers can use flashing lights once they open and are in full control of their canopies. Road flares and other pyrotechnics exude hot melted chemicals while burning and are hazardous when skydivers in freefall use them. In addition, the glare greatly increases the possibility of disorientation.
Additional equipment recommendations include a lighted altimeter, clear goggles, and a flashlight or light on a helmet pointing up to facilitate checking the canopy. A bright LED pointed at the canopy during the entire canopy descent illuminates the parachute for other jumpers, greatly decreasing the chance of a canopy collision. Night jumpers often carry a whistle to warn other jumpers under canopy, signal other jumpers after landing, and to aid rescuers in locating a lost or injured jumper.
Turn your AAD off and back on before beginning night jumps to ensure it is within the time-frame operational limits for the night jump. Drop zone staff should have and check the manifest after night jumps to ensure all jumpers landed safely.
The landing area should contain sufficient lighting—provided by flashlights, electric lights, or similar devices—to illuminate the target. Open flames can be extremely hazardous, so do not use road flares or other pyrotechnics. Car headlights may be used for lighting; however, vehicles clutter the landing area.
E. Procedures
Skydivers should conduct night jumps in light winds and only in clear atmospheric conditions with minimal clouds. Moonlight greatly increases visibility and night-jump safety. USPA recommends jumping during a full moon when conducting group freefall skydives at night. Skydivers should wear white or light-colored jumpsuits.
The BSRs require that you consult the local S&TA or a USPA Examiner for advice for conducting night jumps. Additionally, you may need to notify FAA, state, and local officials as required. Use a topographical map or photo with FAA Flight Service weather information for appropriate altitude and surface winds to compute jump-run compass heading and exit and opening point. One senior member should be designated as jumpmaster for each pass and be responsible for accounting for all members of that pass once everyone has landed. Each jumper performing a night jump who is not familiar with the drop zone should make at least one jump during daylight hours on the same day to become familiar with the drop zone and surrounding areas.
To configure your target for accuracy, arrange lights in a circle around the target area at a radius of 82 feet (25 meters) from the center. Remove three or four of the lights closest to the wind line on the downwind side of the target and arrange them in a line leading into the target area. This will indicate both wind line and wind direction. By following a flight path over this line of lights, the jumper will be on the wind line and land upwind. Place a red light protected by a plexiglass cover at dead center, flush with the surface. In case of emergency, adverse weather or other hazardous jump conditions, extinguish all lights to indicate “no jump.” Ground-to-air radio communications should be available.
Current wind information for both surface and aloft conditions is critical at night to ensure a proper spot. Spotters should familiarize themselves with the drop zone and surrounding area in flight during daylight, noting ground points that will display lights at night and their relationship to the drop zone and any hazardous areas. The spotter should plan to use both visual spotting and aircraft instruments to assure accurate positioning of the aircraft. During the climb to altitude, familiarize each jumper with the night landmarks surrounding the drop zone.
F. Group Jumps: Freefall and Canopy
A person’s first night jump should be solo. On subsequent night jumps, they can make group skydives, starting with a 2-way and then gradually progressing to larger formations. Jumpers should consider staggering their deployment altitudes to reduce the risk of a canopy collision both during deployment and during the canopy descent and landing pattern. When staggering deployments, the jumpers with the lowest wing loadings should deploy at the highest altitude and jumpers should continue in order by wing loading until the jumpers with the highest wing loadings deploy at the lowest altitude.
Once under canopy with others in the air, jumpers should fly predictably and avoid spiraling turns. All jumpers on each pass should agree to the same downwind, base, and final approach and the altitudes for turns to each leg of the landing pattern. Jumpers planning canopy formations should practice together during daylight and rehearse before boarding for each night jump. USPA recommends that skydivers participate in night canopy formations during a full moon. All jumpers should wear brightly colored clothing.